CNC Machining Part Factories: Pioneers in Metal Fabrication
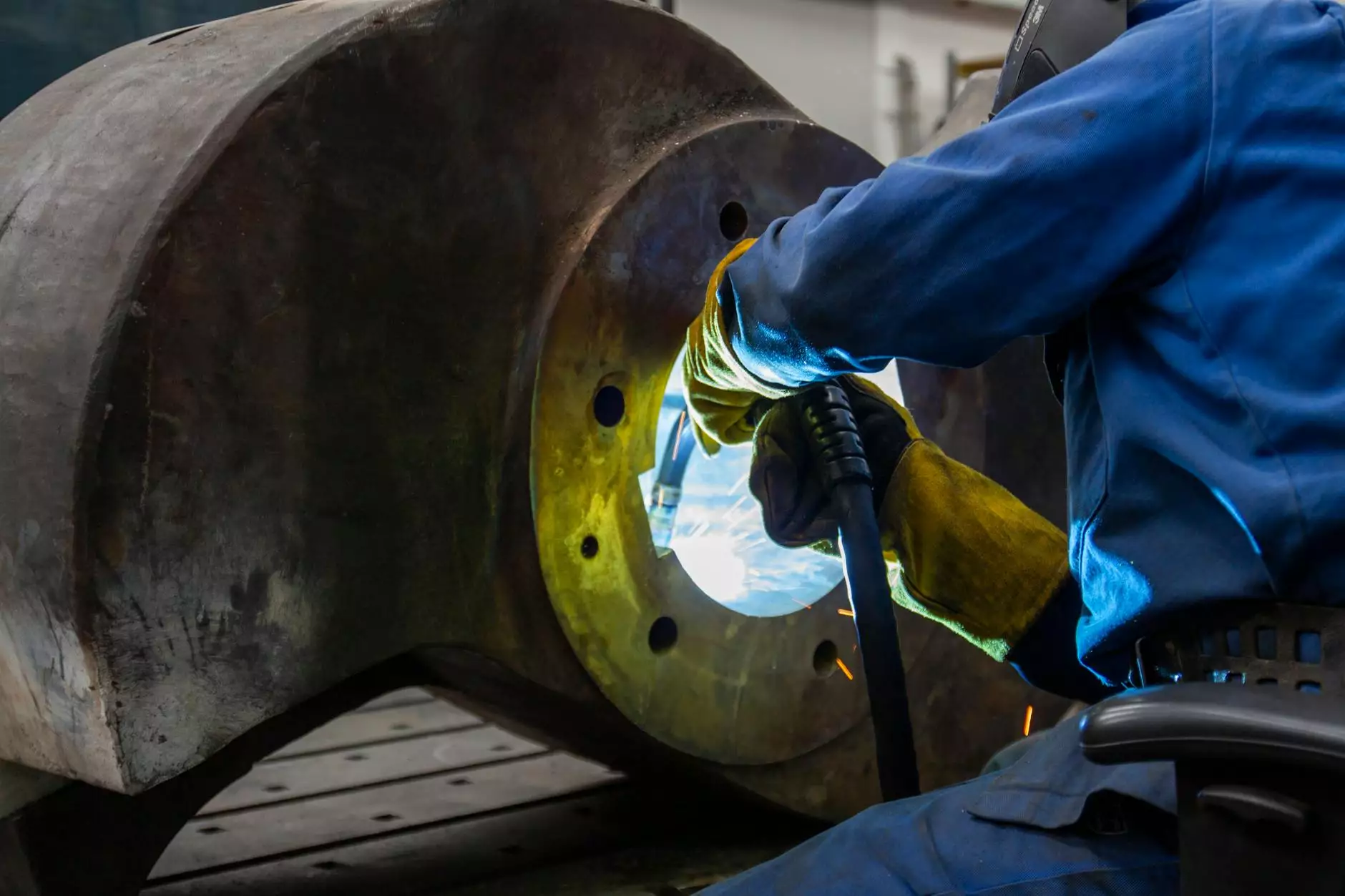
CNC machining part factories represent a critical segment of the manufacturing world, revolutionizing how metal components are produced. With precision engineering and advanced technology, these factories are capable of transforming raw materials into intricate parts that meet the demands of various industries. This article delves into the essentials of CNC machining, its benefits, and its impact on modern manufacturing.
What is CNC Machining?
CNC, or Computer Numerical Control, machining is a method that utilizes computer systems to control machine tools. This process allows for the reliable and precise manufacturing of parts and components, making CNC machining an integral component for industries that demand accuracy.
The Process of CNC Machining
The CNC machining process typically involves several key steps:
- Design Creation: The journey begins with a digital design, often created using CAD (Computer-Aided Design) software. This design outlines the specifications and dimensions of the desired part.
- Toolpath Generation: Once the design is ready, CAM (Computer-Aided Manufacturing) software generates a toolpath that guides the CNC machine on how to cut the material.
- Material Setup: The chosen material, which may include metals such as aluminum, steel, or titanium, is set up within the CNC machine.
- Machining: The CNC machine executes the pre-programmed toolpaths to convert the material into the desired shape through various processes such as milling, turning, and drilling.
- Quality Control: Post-machining, the parts undergo rigorous quality checks to ensure they meet the required specs. This may involve using precision measuring tools and techniques.
Benefits of CNC Machining Part Factories
Establishing a CNC machining part factory comes with numerous benefits, making it a preferred choice for manufacturers around the globe. Some of the key advantages include:
1. Precision and Consistency
One of the most significant advantages of CNC machining is its ability to produce parts with unparalleled precision. The computer-controlled systems ensure that each part is manufactured to the exact specifications, which is crucial in industries such as aerospace, automotive, and medical device manufacturing.
2. Increased Productivity
CNC machines can operate continuously, resulting in 24/7 production capabilities. This constant output dramatically increases productivity compared to manual machining processes. Moreover, the speed at which CNC machines work allows for shorter lead times and faster delivery of products.
3. Versatility in Material Use
CNC machining is not limited to a specific type of material. It can handle a variety of metals and plastics, making it suitable for diverse applications. This versatility is particularly beneficial for metal fabricators who need to cater to different client requirements.
4. Reduced Waste and Lower Costs
Due to its high precision and efficiency, CNC machining minimizes material waste. Parts can be manufactured with close tolerances, leading to less scrap and more cost-effective production processes. This attribute is vital for enhancing profit margins in a competitive market.
5. Complexity Handling
CNC machines can manufacture complex geometries and detailed designs that would be challenging or impossible to achieve with manual methods. This capability opens up vast possibilities for innovation in product design.
Merging Technology with CNC Machining
The rise of technology in CNC machining part factories has transformed traditional manufacturing practices. The integration of various technologies enables factories to become more efficient and forward-thinking:
Automation and Robotics
Many CNC machining part factories are adopting automation solutions, including robotics, to enhance their workflows. Robotic arms can handle loading and unloading processes, ensuring that machines are utilized effectively. This integration not only speeds up production but also reduces human error, leading to higher quality products.
IoT and Smart Factories
The Internet of Things (IoT) has paved the way for the creation of smart factories. In these environments, CNC machines are interconnected, allowing for real-time data sharing and monitoring. This connectivity enables operators to receive immediate feedback on machine performance and condition, leading to proactive maintenance and reduced downtime.
Advanced Software Solutions
Modern CNC machining relies heavily on advanced software solutions that facilitate design, simulation, and production processes. These systems enable engineers to create and optimize designs before production, ensuring potential issues are addressed beforehand.
The Future of CNC Machining Part Factories
The future of cnc machining part factories looks promising as technology continues to evolve. Here are some trends that will shape the industry:
1. Sustainable Manufacturing
As environmental regulations tighten, CNC machining factories are increasingly adopting sustainable practices. This includes using recycled materials and ensuring efficient waste disposal mechanisms. Companies that prioritize sustainability will not only comply with regulations but also appeal to eco-conscious consumers.
2. Customized Production
The demand for customization is growing, and CNC machining allows manufacturers to cater to this need. Factories can lean into producing tailored solutions for their clients without significant increases in costs or time.
3. Integration of Artificial Intelligence
Artificial Intelligence (AI) has the potential to revolutionize CNC machining. With AI, machines can learn from data patterns, allowing for predictive analytics and more optimized machining processes. This intelligence can lead to increased efficiency and reduced operational costs.
4. Enhanced Training Programs
As technologies evolve, so does the need for skilled workers. CNC machining part factories will prioritize training initiatives to ensure their workforce is adept at navigating advanced machinery and software tools. Continuous learning will be vital for maintaining competitive advantages.
Choosing the Right CNC Machining Partner
When selecting a CNC machining partner, several factors should be considered:
- Experience: Look for factories with a proven track record in the industry, as experience often correlates with quality and reliability.
- Capabilities: Assess whether the CNC machining factory has the necessary capabilities to meet your specific production needs.
- Quality Assurance: Inquire about their quality control processes to ensure you receive high-standard products.
- Technological Advancement: A factory that invests in the latest technologies is more likely to deliver efficient and precise manufacturing solutions.
- Customer Support: Exceptional customer service can facilitate smoother communications and project management.
Conclusion: The Impact of CNC Machining Part Factories
The evolution of cnc machining part factories marks a pivotal point in the manufacturing landscape. With their ability to produce high-quality parts efficiently, they continue to serve as a backbone for various sectors, including aerospace, automotive, and healthcare. As technology advances further, these factories will undoubtedly play a crucial role in shaping the future of production, driving innovation, and meeting the complex demands of modern-day industry challenges.
Incorporating CNC machining processes in your manufacturing strategy can yield substantial benefits, making it a wise choice for businesses striving for excellence. As we continue to embrace technological advancements, staying informed and adaptable will be key to success in the dynamic realm of metal fabrication.