Revolutionizing Metal Fabrication with Rapid Prototypes
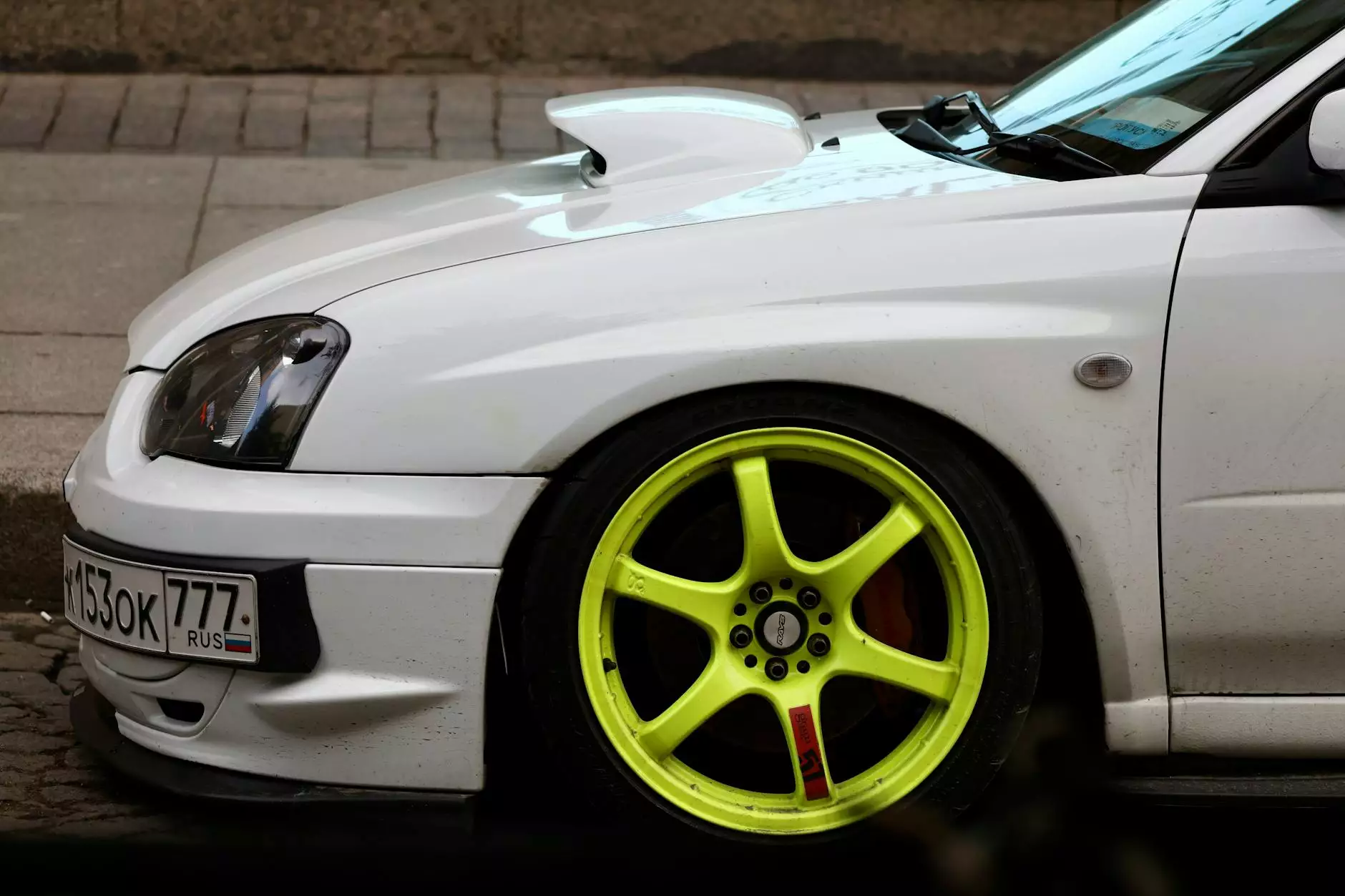
The advancement of technology in the manufacturing industry has brought about significant transformations, particularly in the realm of rapid prototypes. These prototypes have become an essential tool for metal fabricators looking to innovate and streamline their production processes. In this article, we will delve deep into the concept of rapid prototyping, its benefits, applications in metal fabrication, and the future it holds for the industry.
What are Rapid Prototypes?
Rapid prototypes are early-stage models or designs of a product created quickly for testing and validation purposes. They serve as a tangible representation of a concept, allowing businesses to assess form, fit, and function before moving forward with full-scale production. The main objective of rapid prototyping is to shorten the product development cycle, enabling companies to bring their ideas to market more efficiently.
Types of Rapid Prototyping Techniques
There are several methods employed in the creation of rapid prototypes, each with its own unique advantages. Some of the most common techniques include:
- 3D Printing: Also known as additive manufacturing, it involves layering materials to create a three-dimensional object. This method allows for intricate designs and is highly customizable.
- Stereo Lithography (SLA): This process uses a UV light to cure liquid resin into hardened plastic. SLA prototypes boast high accuracy and smooth finishes.
- Selective Laser Sintering (SLS): Similar to SLA, SLS uses a laser to fuse powdered materials into solid structures. This method is particularly effective for strong, functional parts.
- CNC Machining: Unlike additive methods, CNC machining is a subtractive process that uses computer-controlled tools to remove material from a solid block. It’s renowned for precision and durability.
The Importance of Rapid Prototypes in Metal Fabrication
The integration of rapid prototypes into metal fabrication offers numerous advantages that can significantly enhance the overall manufacturing process. Here are some reasons why adopting rapid prototyping is essential for metal fabricators:
1. Accelerated Product Development
One of the most substantial benefits of rapid prototyping is the speed at which companies can develop new products. By utilizing methods like 3D printing and CNC machining, fabricators can produce prototypes in a fraction of the time it would take using traditional methods. This rapid turnaround enables faster testing and iteration, leading to shorter development cycles.
2. Cost-Effectiveness
Producing rapid prototypes can also lead to significant cost savings. By identifying design flaws early in the development process, companies can minimize spending on materials and labor associated with full-scale production. Moreover, the reduction in lead times allows manufacturers to respond quickly to market demands without incurring additional costs for expedited shipping or production.
3. Enhanced Collaboration and Communication
Incorporating rapid prototypes into the design process fosters improved communication among project stakeholders. Having a physical model enables designers, engineers, and clients to visualize the concept accurately, facilitating discussions and allowing for valuable feedback at earlier stages.
4. Increased Innovation
Rapid prototyping encourages creativity and innovation within design teams. The iterative nature of prototyping allows for experiments with various designs and materials without significant investment, leading to groundbreaking products that might not have been developed otherwise.
Applications of Rapid Prototypes in Metal Fabrication
The versatility of rapid prototypes allows them to be applied in various aspects of metal fabrication. Here are some prominent applications:
1. Tooling and Fixtures
Creating tools and fixtures through rapid prototyping can optimize the assembly line process. Custom fixtures can be developed quickly to hold workpieces, ensuring precision and efficiency during production. Tooling made from rapid prototypes can be lighter and easier to handle than traditional metal tools.
2. Product Testing and Evaluation
Prototyping is crucial for testing product designs under real-world conditions. Utilizing rapid prototypes allows engineers to assess the functionality, durability, and performance of a product prior to launching into full-scale production, reducing the risk of costly revisions later in the process.
3. Component Manufacturing
Rapid prototyping can directly contribute to manufacturing components. For instance, smaller production runs that require unique parts can benefit from creating prototypes that can be produced on-demand, which enhances flexibility and responsiveness to customer needs.
4. Replacement Parts Production
In industries that rely heavily on machinery, the ability to quickly produce replacement parts is invaluable. Rapid prototyping allows for the on-demand manufacturing of parts that may no longer be readily available, reducing downtime and maintaining operational efficiency.
The Future of Rapid Prototypes in Metal Fabrication
As technology continues to evolve, the future of rapid prototypes in metal fabrication looks promising. Emerging trends such as advanced materials, automation, and artificial intelligence are set to enhance the capabilities and applications of rapid prototyping:
1. Advanced Materials
New materials are consistently being developed that improve the strength, weight, and finish of prototypes. For example, metal 3D printing has opened doors to creating complex geometries that were once thought impossible with traditional methods.
2. Automation and AI
Integrating automation and AI into the prototyping process will allow for smarter production and improved efficiencies. Predictive analytics can help in forecasting demands, optimizing production schedules, and enhancing quality control during the prototyping phase.
3. Sustainability
With growing environmental concerns, the future of rapid prototyping is leaning towards sustainability. Techniques that minimize waste and utilize recyclable materials are in development, making metal fabrication processes more eco-friendly.
Conclusion
The role of rapid prototypes in metal fabrication cannot be overstated. As companies strive for excellence in product development and manufacturing efficiency, embracing rapid prototyping technologies will prove essential. By leveraging the speed, cost-effectiveness, and innovative potential of prototyping, businesses like DeepMould.net can stay ahead of the competition and meet the ever-changing demands of the market. The future is bright for those willing to invest in rapid prototyping as a cornerstone of their manufacturing processes—enabling unparalleled creativity and efficiency in metal fabrication.